これは、実装、検査調整、メンテナンスなどの作業補助のためです。
最近では実装密度が高くなり、シルク印刷の表示も工夫が必要になっています。
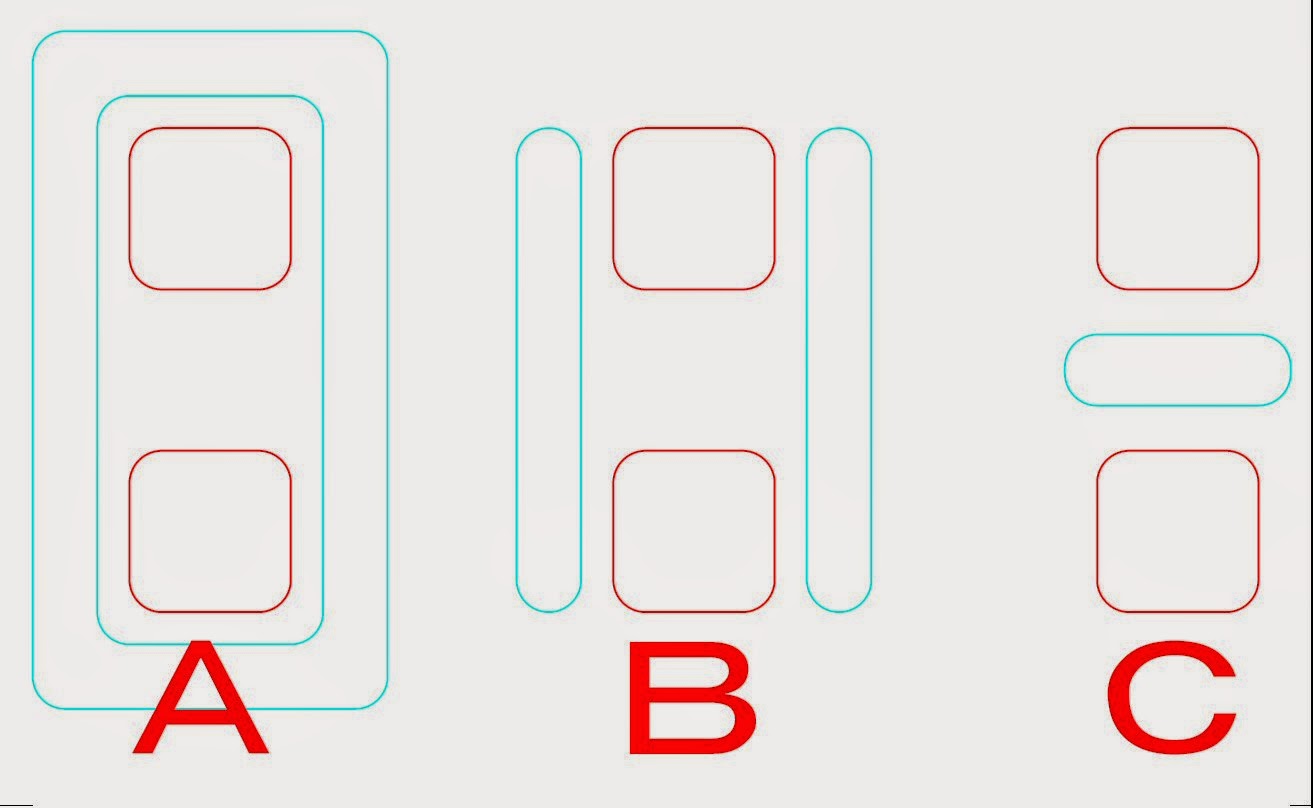
印刷の表示が多いと思います。
(A)は確実に位置が決まりますが、
基板の面積を多く取るので、
実装密度が高い場合は(B)や(C)が
使われます。
(C)の場合、チップの周りのスペースは
使いませんが、部品の下のシルクインクが
問題になることがあります。

1005チップコンデンサに(C)のシルク印刷した場合、シルクインクの上にチップが乗り上げた状態になります。
(ハンダペーストは描いていません)
レジストの銅箔上の厚さ10μmとし、シルクインクの厚さ20μmとすると基板パットとチップ電極の隙間は約30μm
銅箔パターン厚さ:18μm
レジスト厚さ:20~40μm
シルクインク厚さ:20~40μm
チップがペーストハンダ溶解時に傾くことが稀にあります。
この場合、開いた側の間隔は最大60μmと
なり,100~120μmのステンシルで印刷した場合ペーストはんだの厚さが60~70μmですから、半田から離れてしまう可能性があります。
このような不安定な状況は避けた方が
よいと思います。